Comprehensive Guide to Tank Welding Inspection for Safety And Security and Top quality
Wiki Article

Understanding the Importance of Rigorous Container Welding Evaluation Processes in Preventing Failures and Enhancing Life Expectancy
In the realm of commercial procedures, the importance of rigorous container welding examination procedures can not be overemphasized. By executing various inspection methods, companies can identify flaws early, consequently staying clear of expensive repercussions and extending the life of their storage containers.Value of Welding Evaluations
Recognizing the vital duty of welding inspections in preserving structural integrity, these procedures guarantee that welds fulfill well-known requirements and specifications - Tank Welding Inspection. Effective welding inspections are critical in the construction and upkeep of containers, as they directly affect the sturdiness and security of the structures. By recognizing potential deficiencies, such as improper techniques or material issues, examinations minimize the danger of tragic failingsWelding inspections encompass numerous methodologies, including visual evaluations, non-destructive testing (NDT), and assessments of welding treatments. Each method offers to validate the high quality and compliance of welds with market laws, thereby protecting both employees and environmental interests. Normal inspections foster a culture of responsibility and quality within the labor force, ensuring that all group members stick to ideal practices.
Furthermore, these assessments add to the overall lifecycle administration of storage tanks by identifying wear or destruction early at the same time. By resolving these issues proactively, organizations can extend the operational life-span of their assets, eventually leading to set you back savings and enhanced integrity. In summary, the value of welding evaluations can not be overemphasized; they are crucial for guaranteeing security, longevity, and conformity in storage tank building and construction and maintenance.
Common Reasons For Container Failures
Comprehending the typical reasons of container failings is crucial for preventing devastating cases and making sure the long life of storage space systems. One common reason for storage tank failing is corrosion, which can dramatically compromise the structural integrity of storage tanks with time. Environmental factors, such as direct exposure to wetness, chemicals, and temperature changes, can accelerate this procedure.An additional essential variable is improper welding techniques, which might result in issues like cracks or insufficient joints. These problems can compromise the container's toughness and result in leakages or ruptures. Additionally, inadequate maintenance techniques can cause unnoticed damage, eventually increasing the risk of failure.
Design imperfections, including insufficient density or poor product option, can additionally add to container susceptabilities. In addition, operational aspects, such as overfilling or direct exposure to extreme stress, can strain the storage tank beyond its designated limitations.
Secret Examination Methods
Reliable examination strategies play an essential duty in mitigating the threats related to container failures. An extensive approach to tank welding inspection entails several key techniques, each created to identify possible defects and make certain architectural stability.Aesthetic evaluation stays the initial line of protection, enabling assessors to determine surface area abnormalities such as splits, deterioration, or misalignment. This technique is frequently supplemented by non-destructive testing (NDT) approaches, which are necessary for analyzing weld high quality without endangering the tank's honesty.
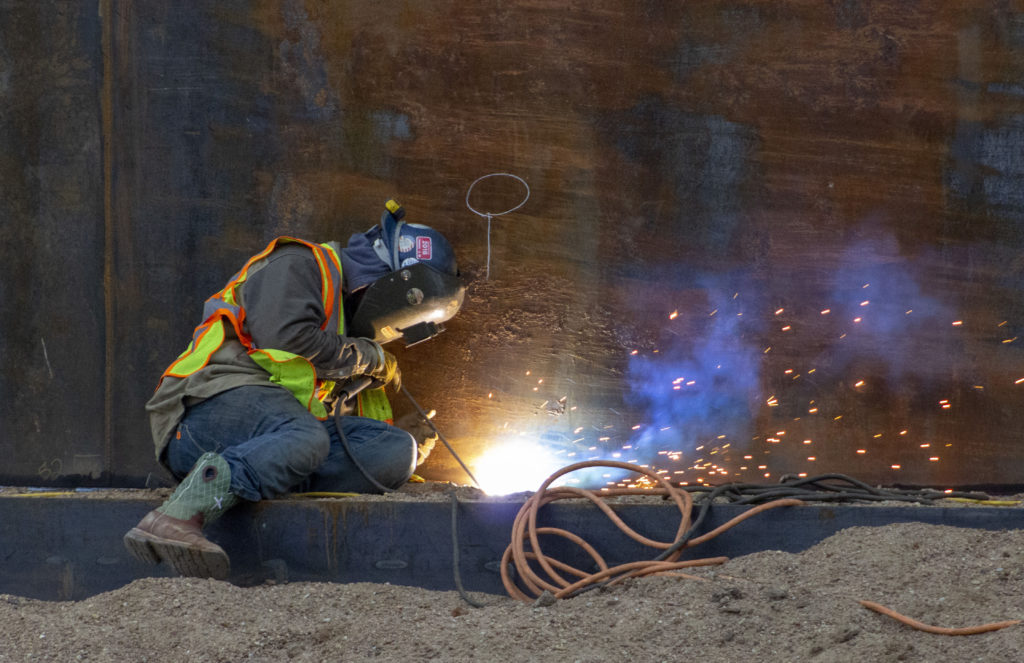
In addition, magnetic bit testing (MPT) and dye penetrant screening (DPT) are reliable for identifying surface defects in ferromagnetic materials and non-porous surfaces, specifically. Each technique has its toughness and constraints; consequently, a mix of techniques is commonly utilized to achieve detailed inspection results.
Advantages of Rigorous Examinations
While the immediate prices of rigorous evaluations may appear challenging, the long-term advantages considerably outweigh these preliminary investments. Carrying out thorough evaluation refines not just enhances the stability and security of container structures but also lessens the risk of devastating failings that can result in considerable monetary losses and environmental damage.
Extensive evaluations help identify possible issues early in the welding process, enabling for prompt rehabilitative activities that prevent expensive repair work or substitutes down the line. This proactive approach promotes a society of quality guarantee, where adherence to ideal practices becomes instilled in operational treatments. Routine examinations add to boosted possession longevity, as they ensure that storage tanks stay in optimal problem throughout their life expectancy.
Furthermore, the documentation created from these evaluations serves as a beneficial source for upkeep preparation and efficiency evaluations. This data-driven method can also improve operational performance, causing decreased downtime and enhanced efficiency. Inevitably, rigorous evaluations not only guard the structural honesty of tanks however also give substantial financial benefits, reinforcing the notion that buying quality control is a sensible choice for any type of company involved in storage tank operations.
Regulative Requirements and Conformity
Governing standards and conformity are necessary parts of tank welding evaluation procedures, as they develop the structure for ensuring safety and security and high quality in operations. Conformity with these standards not only alleviates link dangers yet likewise improves the overall integrity of bonded frameworks. Numerous companies, including the American Society of Mechanical Designers (ASME) and the American Petroleum Institute (API), give standards that dictate acceptable methods for welding, inspection, and screening.These criteria mandate making use of certified employees, the implementation of extensive examination methods, and adherence to specific welding procedures. By lining up with governing needs, companies can ensure that their containers satisfy the required safety and security and performance standards, thereby reducing the likelihood of catastrophic failures that can result in considerable economic losses and environmental damages.

In addition, regulatory conformity fosters a culture of accountability and continuous renovation within the welding and fabrication industries (Tank Welding Inspection). Routine audits and inspections guarantee that techniques continue to be lined up with evolving i loved this standards, therefore promoting long-term dependability and functional performance. Ultimately, adherence to governing standards not only shields browse around this site assets however likewise boosts the lifespan of bonded storage tanks, ensuring they serve their intended objective successfully with time
Conclusion
In conclusion, strenuous storage tank welding evaluation procedures play an essential role in avoiding failures and prolonging the lifespan of storage space frameworks. By recognizing potential deficiencies through different assessment strategies, organizations can minimize dangers associated with container stability.Report this wiki page